What Are Metal Domes?
Metal domes also called snap dome or dome metals. They are small, spring-like components typically made from high hardness stainless steel such as SUS301 or SUS304. Snap domes are designed to deform under pressure and snap back to their original shape.
The metal dome is a normally-open tactile switches, when pressed, the domes collapse and make contact with the secondary pathway, thereby closing the circuit. These metal domes are an essential part of membrane switches, providing not only tactile feedback but also contributing to the overall durability and functionality of the switch.
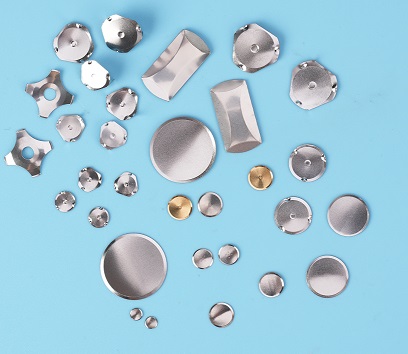
What Is a Metal Dome Array?
A metal dome array consists of multiple metal domes arranged in a specific sheet, so it is called metal dome sheets as well. They use PET glued adhesive tape as the base, and metal domes sticked on the top of PET, when used, customers can peel a full sheet of metal dome onto their device. These arrays are integrated into membrane switches to allow for multiple button presses in a compact space.
The metal domes in the array are positioned in a way that ensures each dome functions independently. This configuration makes the array highly effective in providing precise tactile feedback and long-lasting performance. Essentially, a metal dome array allows for consistent functionality, no matter how frequently the switch is pressed.
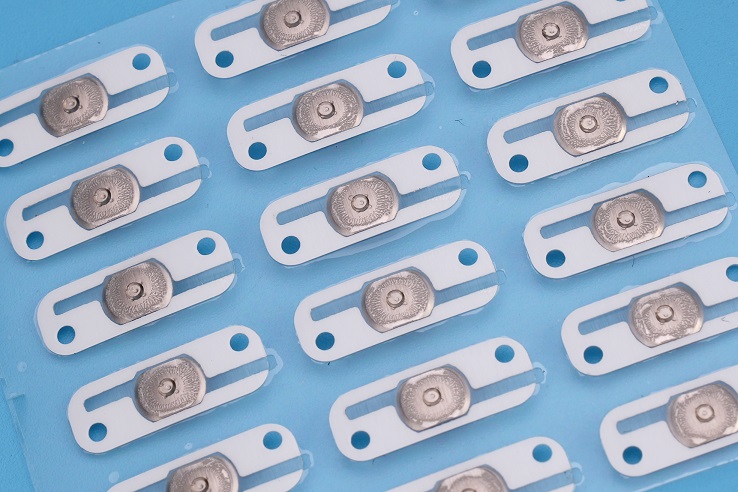
How Does a Metal Dome Array Work in a Membrane Switch?
In a membrane switch, the metal dome array is placed between the printed circuit board (PCB) and the top layer of the switch. When a button is pressed, the pressure causes the metal domes to deform. This deformation activates a circuit beneath the dome, completing the electrical connection and signaling the action to the device. Once the pressure is released, the dome returns to its original shape, breaking the connection and providing tactile feedback to the user.
The effectiveness of a metal dome array lies in its ability to create a distinct and reliable actuation process, ensuring the user gets a clear indication that their input has been registered. The tactile response from the metal dome array also adds to the overall user experience by enhancing the feel of the switch.
Types of Metal Domes
1. T-Series Metal Dome
T-series metal dome full name is triangle metal dome. It is triangle shaped metal dome which is designed for mounting on single or double sided printed circuit boards, flex circuits and membranes, where a Via is run through the circuit board. They are typically used in applications where clear and precise feedback is essential, such as in industrial control panels or consumer electronics.
2. F-Series Metal Dome
The F-series metal domes have four legs, so it is called four legs metal domes. They are similar to the T-series but are designed to offer a softer tactile feedback. The size of F series metal dome is from 5mm to 20mm in a range of (trip) force, typical 125- 500 gf. They are often used in applications where a lighter touch is required, such as in handheld devices or certain consumer appliances.
3. C/R-Series Metal Dome
The circle/round-series metal domes has a round shaped and known for their high durability and resistance to wear and tear. These domes are typically used in environments where switches undergo heavy usage or are exposed to extreme conditions, such as medical devices, automotive systems, or industrial machinery.
4. O-Series Metal Dome
The Oblong-series metal domes are often used in applications that require a more tactile, “clicky” feel. The O-Series metal domes can be used in a long & narrow space than other three shape domes. The size for small one is like 3*4mm, 3.7*5.0mm, 4.2*5.6mm, and medium one as 7.1*8.9mm, 5.6*11.28mm, 8.89*17.78mm, and bigger one can be 12.7*25.4mm, 38.1*12.8mm, even 51*13.70mm. Sometimes people also call it “rectangle dome”.
5. Custom Shaped Metal Dome
For specialized applications, custom-shaped metal domes can be designed to meet unique requirements. These domes can be tailored to fit specific sizes, shapes, and actuation forces, allowing for a highly customized membrane switch solution. Custom-shaped domes are often used in high-end consumer electronics or applications where the form factor is critical. They offer the flexibility to design switches that perfectly match the desired user experience, whether for aesthetics or functionality.
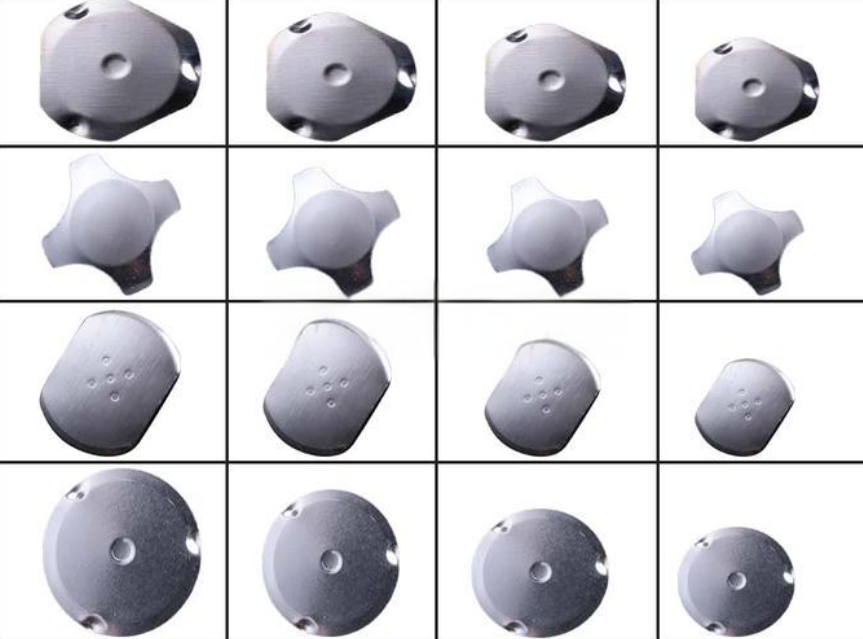
The Benefits of Metal Dome Arrays
There are several advantages to using metal dome arrays in membrane switches. One of the most significant benefits is their tactile feedback. The “click” produced when a metal dome is pressed ensures that the user knows their input has been received. This feedback is especially important in applications where precision is key.
Another major benefit is the durability of metal dome arrays. These components are highly resistant to wear and tear, making them ideal for use in environments where switches are used frequently. Metal domes can withstand millions of presses without losing their functionality, which is crucial for industries such as automotive or medical equipment, where reliability is critical.
Metal dome arrays also contribute to the slim profile of membrane switches. By using a compact array of domes, manufacturers can create switches that are both functional and space-efficient. This is particularly important in applications where space is limited, such as in handheld devices or control panels.
Metal Dome Array Use Cases
- Consumer Electronics
- Automotive Control Panels
- Medical Devices
- Industrial Equipment
- Consumer Appliances
- Aerospace
- Control panel device
- Military
- Oil and Gas
- Transportation
How to Choose the Right Dome for a Membrane Switch?
Choosing the right metal dome for your membrane switch is crucial for ensuring performance, durability, and user satisfaction. Here are a few factors to consider:
- Size: The size of the film button should meet the national standard, generally 35mm long, 15mm wide, 1mm high.
- Thickness: The thickness of the thin film button is generally 0.025mm-0.035mm, and the accuracy of the thickness is within 0.003mm.
- Strength: The strength of the film button should meet the national standard, generally 2.5N. Strength testing requires the use of specific test equipment.
- Shape: The shape of the dome will affect how it fits within your membrane switch design.
- Environment Factor: Consider the environment in which the switch will be used. If the switch will be exposed to extreme temperatures, humidity, or chemicals, choose metal domes that are resistant to these factors.
Best Technologty is a professional and experienced company that specializes in designing and manufacturing custom metal dome and metal dome arrays. We have our own metal dome factory and membrane switch factory in China. If you would like more information about metal domes and how they can enhance your user experience, please get in touch with us at your convenience, we can arrange meeting or arrange visit with you.