Keyboards have come a long way from simple input devices to something that reflects personal style and functionality. In recent years, the inclusion of RGB LED lighting has become a common feature in many keyboards. Whether it’s for gaming, work, or just personal preference, LED lighting allows users to customize their keyboards in ways that were once unimaginable. But this leads to a pressing question: Do LEDs on keyboards make them hot? This question is of particular concern to gamers, typists, and anyone who spends extended hours using their keyboards. After all, the last thing anyone wants is a keyboard that heats up and becomes uncomfortable to use. In this article, we’ll break down how LEDs work, explore whether they affect the temperature of your keyboard, and discuss other factors that might contribute to your keyboard heating up.
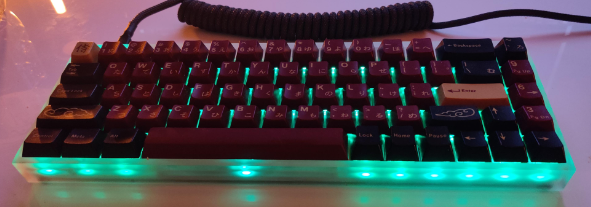
How Do LED Lights on Keyboards Work?
LEDs, or Light Emitting Diodes, are a type of light source that generate light when an electric current passes through a semiconductor material. Unlike traditional incandescent light bulbs, which rely on heating a filament to produce light, LEDs create light through a process called electroluminescence. When electricity flows through the LED’s semiconductor material, it emits photons (light particles), which we see as visible light.
On keyboards, these tiny LEDs are strategically placed beneath each key or along the frame to provide backlighting or RGB effects. The small size of the LEDs and their ability to produce bright light with minimal power consumption make them ideal for modern keyboards. They create the colorful, customizable lighting effects that many users enjoy without requiring excessive power or generating a significant amount of heat.
Are LEDs in Keyboards Energy-Efficient?
Absolutely. LEDs are some of the most energy-efficient lighting options available today. They require very little power to operate, making them a preferred choice for modern electronics. In a typical keyboard, the LEDs’ power consumption is minimal when compared to the overall power usage of the device.
For example, even a fully illuminated RGB keyboard, with all keys glowing brightly, would still consume very little electricity. When you think about it, the power usage for a single key’s LED might be comparable to that of a small light bulb or less. In the grand scheme of things, the total power consumption from the LEDs is a fraction of what is needed for other components like the processor, display, or computer’s cooling system.
Can LED Lighting on Keyboards Cause Overheating?
The simple answer is: No, LEDs in keyboards do not cause overheating. In fact, the heat generated by LEDs is negligible. The LEDs in keyboards are designed to emit very little heat due to their energy efficiency and low power requirements. As a result, they are not a source of concern when it comes to raising the temperature of your keyboard.
Keyboards are designed with thermal management in mind, ensuring that even if the LEDs are used extensively, the device remains at a comfortable temperature. Keyboards with built-in LED lighting are generally equipped with materials that help dissipate any heat that may be produced. Plastic casings, metal frames, and specialized ventilation areas ensure that any heat produced by the device is quickly dispersed, maintaining an ideal operating temperature for the keyboard.
Even when the lights are set to maximum brightness, the amount of heat produced is still so minimal that it does not cause any noticeable increase in the keyboard’s temperature. If you do feel warmth in your keyboard, it is most likely due to other factors, such as the external environment or the power load being placed on the device, rather than the LEDs themselves.
What Factors Can Cause a Keyboard to Heat Up?
While the LEDs themselves aren’t responsible for heating up your keyboard, there are a few other factors that might contribute to warmth. Understanding these factors will help clarify why a keyboard might feel warm at times.
1. External Temperature and Environment
The temperature of your room or the area where you’re using the keyboard can play a significant role in how warm your keyboard feels. If you’re working or gaming in a particularly hot room, it’s natural for your keyboard to feel warmer, especially if it’s been in use for several hours. High ambient temperatures can cause keyboards to retain more heat and feel uncomfortable.
2. Device Power Usage
While LEDs consume very little power, other components of your computer or keyboard may contribute to the heat. If you’re using a gaming keyboard with additional features like mechanical switches, RGB lighting, or built-in screens, these devices might require more power to operate. The power demand from other high-performance components could lead to an overall increase in temperature, which can be felt in your keyboard.
3. Poor Ventilation
A lack of ventilation is another factor that can cause keyboards to heat up. If your workspace is cluttered or your computer is placed in a confined space, heat may become trapped around the keyboard, causing it to feel warmer than usual.
How Does LED Color Affect Heat in Keyboards?
One common misconception is that certain LED colors might generate more heat than others. However, this is not true. The color of the light emitted by the LED does not have a significant impact on how much heat it produces.
Most RGB LEDs in keyboards operate using red, green, and blue light sources. These LEDs combine to create a full spectrum of colors, which can range from cool blues to warm reds. But regardless of the color, the underlying mechanism that powers these LEDs is the same. The power consumption remains low across all colors, and the light emitted is efficient and cool to the touch.
So, whether your keyboard is glowing with vibrant blues or warm reds, the heat generated by the LEDs remains virtually the same. The color only affects the visual aesthetic of the keyboard and not its thermal performance.
Do Keyboards with RGB Lights Heat Up More Than Standard Keyboards?
RGB keyboards might seem like they would generate more heat because they feature multiple colors and elaborate lighting effects. However, in terms of actual temperature, RGB keyboards behave in much the same way as single-colored LED keyboards. The key difference lies in the customization options—RGB keyboards allow users to create an array of dynamic lighting patterns and colors, but they don’t require significantly more power to operate.
The truth is, RGB lighting doesn’t demand any more power than a single color LED does. The added lighting effects are typically controlled by the keyboard’s software and involve alternating between different colors and brightness levels. However, this switching effect doesn’t increase the power usage enough to cause any significant rise in temperature. Therefore, whether your keyboard is equipped with RGB lights or single-color LEDs, the heat generated will be minimal.