What is a Force-Displacement Curve?
What is a Force-Displacement Curve? A force-displacement curve is a graphical representation that shows the relationship between the applied force and the resulting movement or displacement of a material or object. When it comes to tactile dome switches, this curve plays a critical role in understanding the physical behavior of the switch when it is pressed. It allows manufacturers to gauge how much force is required to activate the switch, how the switch responds to the applied force, and how the switch behaves after it is released.
The graph typically features key points, including the actuation force, which represents the force required to activate the switch, and the return force, which indicates how much force is needed to reset the switch after use. These data points are important because they help in fine-tuning the switch’s tactile response.
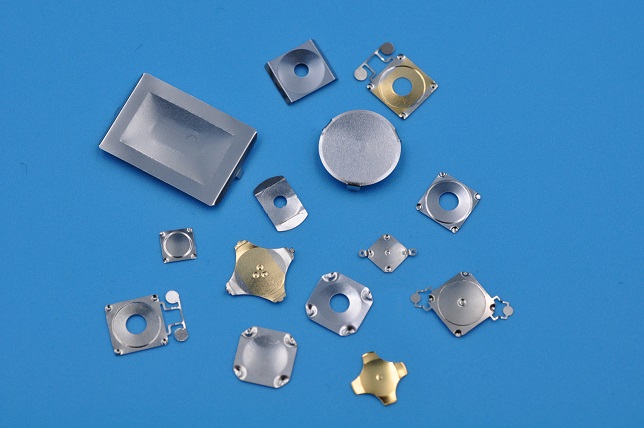
How to Read a Switch Force Graph?
Reading a switch force graph is a straightforward process once you understand its key components. The force graph starts at the origin point (0,0), where no force is applied and no displacement occurs. As you begin to apply force to the tactile dome switch, the graph rises gradually. This section of the curve represents the initial movement of the dome as it deforms under the applied force. The slope of the curve here can tell you how easy it is to press the switch and how much resistance the switch offers during this phase.
At some point, the curve reaches its peak, which represents the actuation force — the point at which the switch is activated and the circuit underneath is closed. After the peak, the curve drops sharply, representing the tactile feedback or “click” that occurs when the switch is fully engaged.
As the force is released, the graph moves back down, showing the return force. This portion of the graph reflects how the dome switch returns to its original shape and resets the circuit. The return force is usually slightly less than the actuation force, indicating that it requires less effort to release the switch than to press it.
How Does a Dome Switch Work?
A tactile dome switch operates using a simple but effective mechanism that involves a flexible, dome-shaped component, this is we called metal dome or snap dome. The dome is typically made from metal materials like stainless steel, often used SUS304 or SUS301 stainless steel. When a user applies force to the dome, it deforms, compressing the dome and pushing it downwards. This movement closes the electrical circuit underneath, sending a signal to the device or system that the switch has been activated.
Once the force is released, the dome returns to its original shape, opening the circuit again. This action creates the “click” sound and tactile response that users feel when the switch is pressed. The material of the dome and its shape are carefully designed to ensure that the switch provides a satisfying tactile response, signaling to the user that the switch has been engaged successfully.
Dome switches are popular in various applications because they are compact, reliable, and cost-effective. They are commonly used in electronics, automotive controls, and even household appliances. The simplicity of the dome switch design makes it ideal for applications where space is limited or where users need a clear and tactile indication of activation.
How to Test a Force-Displacement Curve?
Testing a force-displacement curve requires specialized equipment to apply controlled force to the tactile dome switch and measure the resulting displacement. The most commonly used equipment for this purpose is a force gauge or a universal testing machine (UTM). These machines are capable of applying a steady and controlled amount of force to the switch while recording the data on a graph.
During the curve testing, placing dome switch securely in the testing machine to prevent any unwanted movement. The machine then applies force to the dome at a controlled rate, pressing it down while simultaneously recording the force and displacement at various points. The resulting data is plotted on a graph, showing how the switch behaves under different levels of pressure.
During testing, key points such as the actuation force, peak force, and return force are analyzed to determine the performance of the switch. Once the force-displacement curve is generated, repeated tests are often performed to assess the switch’s consistency and reliability.
How to Convert a Force-Displacement Curve to a Stress-Strain Curve?
Converting a force-displacement curve to a stress-strain curve is a process that involves calculating two key parameters: stress and strain. While the force-displacement curve gives us valuable data about how force is applied to the switch and how it displaces, a stress-strain curve provides insight into how the material behaves internally under that force. Here’s how you can convert the data from one to the other:
1. Collect Data from Force-Displacement Curve:
Start by gathering data points from the force-displacement curve that show the force applied to the tactile dome switch and the resulting displacement (or movement) of the dome. Please noted: force (in Newtons, N) and displacement (in millimeters, mm).
2. Determine the Cross-sectional Area of the Dome:
To convert force into stress, you need to know the cross-sectional area of the dome material. This is typically determined by the shape and dimensions of the dome.
For example, if the dome is circular, you can calculate the cross-sectional area using the formula:
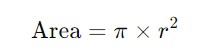
Where r is the radius of the dome’s cross-sectional area.
If the dome is flat or has a different shape, adjust the area calculation accordingly.
3. Calculate Stress:
Stress is the force applied per unit area of the material. Once you have the force (F) and the cross-sectional area (A), you can calculate stress (?) using the formula:
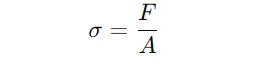
where: ? is stress (in Pascals, Pa), F is the force (in Newtons, N), A is the cross-sectional area (in square meters, m²).
4. Calculate Strain:
Strain is the deformation or displacement of the material relative to its original length. For this, you need the original length (L) of the dome before any force is applied. The strain (?) is calculated using the formula:
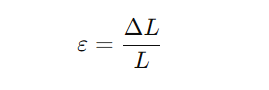
where: ? is strain (dimensionless), ?L is the displacement (change in length) (in meters, m), L is the original length of the dome (in meters, m).
- Plot the Stress-Strain Curve:
- Once you have calculated stress and strain for each data point from the force-displacement curve, plot these points on a new graph.
- On the x-axis, plot strain, and on the y-axis, plot stress.
- As you plot the points, you will see the material’s behavior under increasing force and deformation, which will help in evaluating the material’s elastic and plastic regions.
FAQs
1. What materials are used in tactile dome switches?
Tactile dome switches are typically made from stainless steel, which offers durability and flexibility.
2. Can force-displacement curves predict switch lifespan?
Yes. By testing the switch’s performance under repeated force cycles, manufacturers can estimate the switch’s lifespan and identify any potential failure points.
3. What factors affect a dome’s actuation force?
The thickness of the material, the shape of the dome, and the overall design of the switch all influence the actuation force.
4. Are all force-displacement curves the same?
No. Each tactile dome switch is designed for specific applications and has its own unique force-displacement curve.
5. Why is tactile feedback important?
Tactile feedback ensures that users can feel when a switch has been activated, improving the user experience and preventing errors.